Browsing the World of Welding Services: A Comprehensive Guide to Types and Benefits
In the world of commercial applications and building and construction projects, the relevance of welding solutions can not be overstated. As we get started on this comprehensive guide to the types and benefits of welding solutions, we will certainly delve right into the ins and outs of various welding processes, discover the advantages of MIG and TIG welding, and lost light on the specialized methods that provide to distinct tasks.

Various Sorts Of Welding Procedures
Different methods are employed in welding processes to join materials together effectively and securely. One common welding technique is Shielded Steel Arc Welding (SMAW), also known as stick welding. This process makes use of a flux-coated palatable electrode to create the weld. SMAW is flexible and can be made use of in numerous placements, making it popular in construction and repair service job.
An additional widely made use of method is Gas Steel Arc Welding (GMAW), or MIG welding. In this process, a cable electrode is fed via a welding weapon, which likewise releases a protecting gas to protect the weld from contaminants airborne. GMAW is understood for its speed and convenience of use, making it appropriate for manufacturing and automobile sectors.
Moreover, Gas Tungsten Arc Welding (GTAW), or TIG welding, is preferred for its precision and tidy welds. If required, TIG welding makes use of a non-consumable tungsten electrode and a separate filler product. This technique is commonly utilized in aerospace, automobile, and imaginative applications due to its ability to develop premium welds
Benefits of MIG Welding
MIG welding, additionally called Gas Steel Arc Welding (GMAW), offers distinctive advantages over various other welding processes, making it a preferred choice in production and automotive markets. One of the key benefits of MIG welding is its versatility. This process can be utilized on a variety of metals and densities, consisting of aluminum, stainless-steel, and light steel. Furthermore, MIG welding is understood for its high welding rates, resulting in boosted productivity. The procedure is fairly very easy to implement and find out, making it ideal for both novices and skilled welders.
In addition, MIG welding produces clean welds with very little spatter, decreasing the requirement for considerable post-weld cleaning. Making use of a protecting gas in MIG welding secures the weld pool from pollutants in the setting, leading to top quality, strong welds. Another benefit of MIG welding is its ability to be automated, enabling precise and consistent welds in automation setups. On the whole, the advantages of MIG welding make it a popular selection for different applications where effectiveness, quality, and simplicity of usage are essential.
Advantages of TIG Welding
Tungsten Inert Gas (TIG) welding, likewise recognized as Gas Tungsten Arc Welding (GTAW), sticks out in the welding sector for its exact control and top quality welds. One of the primary advantages of TIG welding is its ability to create clean and aesthetically pleasing welds without the requirement for filler material. This leads to welds that need minimal post-weld cleaning and polishing, making TIG welding perfect for applications where look is crucial.
Moreover, TIG welding is fit for welding slim materials as a result of its reduced heat input and accurate control over the welding arc. This makes it a recommended option for markets such as aerospace, auto, and electronics, where welding slim sections without distortion is important.
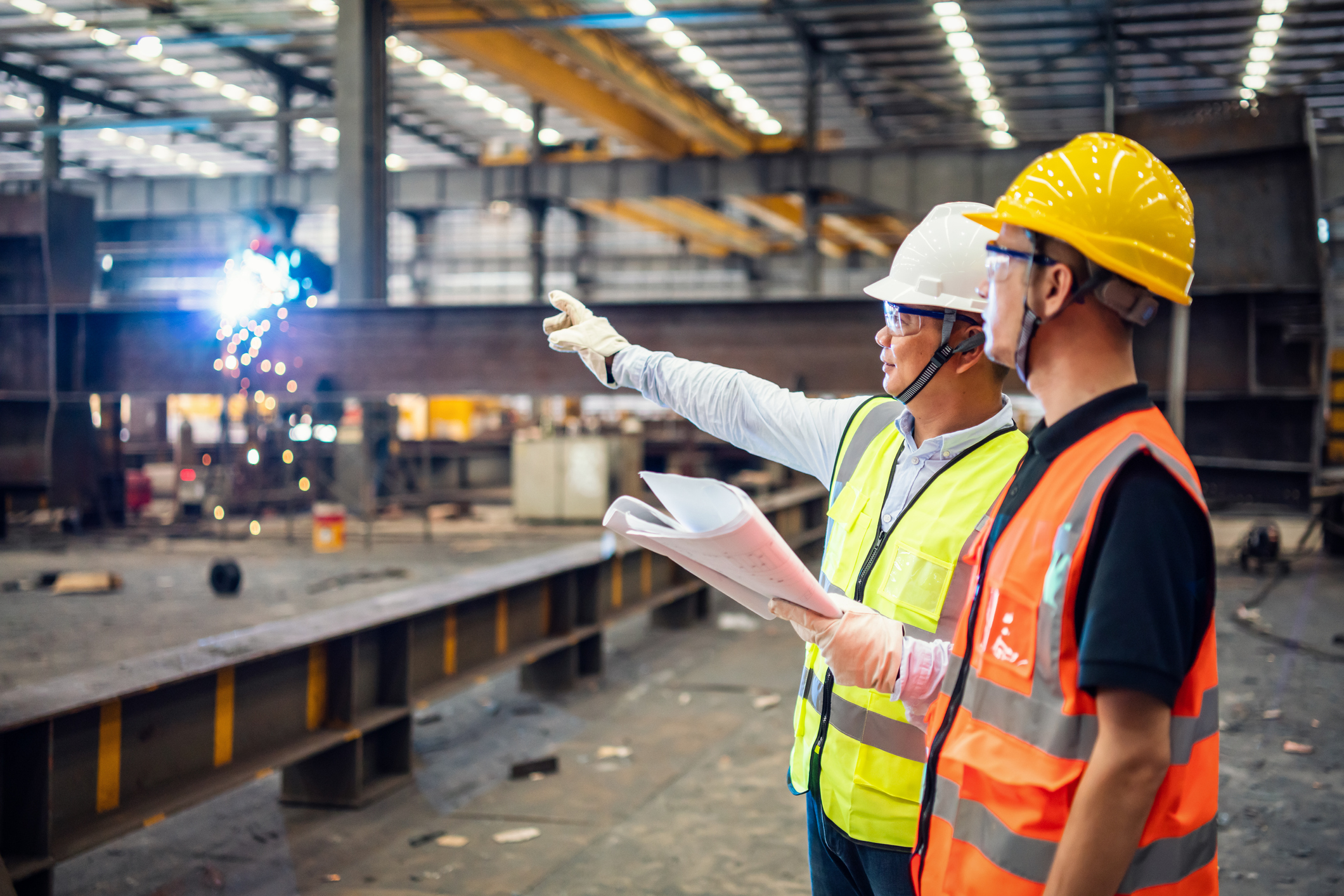
Checking Out Arc Welding Techniques
When diving right into the world of welding techniques, one comes across a varied range of arc welding techniques that play a vital role in various industrial applications. Arc welding is a commonly used welding procedure that entails creating an electrical arc in between an electrode and the base product to melt and sign up with steels. Welding Inspection Service. One of the most common arc welding techniques is Protected Metal Arc Welding (SMAW), also recognized as stick welding, which is preferred for its convenience and simplicity. SMAW is suitable for welding thick products and can be used both inside and outdoors, making it a prominent selection in construction and pipe welding.
An additional prevalent arc welding approach is Gas Metal Arc Welding (GMAW), frequently referred to as MIG (Metal Inert Gas) welding. GMAW utilizes a consumable cable electrode and a protecting gas to protect the weld swimming pool from climatic pollutants, leading to high-grade welds with very little spatter. This strategy is commonly used in automobile, production, and manufacture sectors for its effectiveness and simplicity of usage. Overall, arc welding strategies provide a variety anonymous of alternatives to accommodate varied welding needs throughout different sectors.
Understanding Specialized Welding Provider
Specialized welding services play an important role in fulfilling the one-of-a-kind needs of complex industrial projects and accuracy applications. These services surpass typical welding techniques to address specific difficulties that conventional approaches may not effectively fix. Specialized welding incorporates a variety of advanced processes tailored to satisfy the needs of specialized sectors such as aerospace, automobile, and manufacturing.
One trick facet of specialized welding services is the capacity to deal with exotic products that need customized knowledge and equipment. This consists of welding procedures for materials like titanium, magnesium, and numerous high-strength alloys, which require a high level of skill and precision to make sure optimal outcomes.
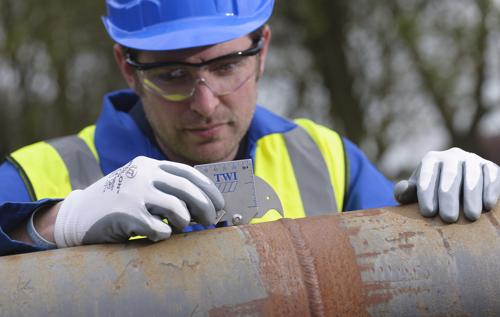
Basically, specialty welding solutions are important for markets that require the highest possible requirements of quality, durability, and precision in their welding tasks. By leveraging specialized strategies and knowledge, these solutions enable organizations to deal with complex obstacles and accomplish remarkable results in their procedures.
Conclusion
In conclusion, understanding the various kinds of welding procedures and their benefits is necessary for navigating the world of welding services. MIG welding provides advantages such as high performance and simplicity of use, while TIG welding provides benefits like specific control and tidy welds. Discovering arc welding strategies and specialty welding solutions can further expand the alternatives and capacities offered for various welding tasks. By familiarizing oneself with these different alternatives, people can make informed decisions when choosing welding services.
As we embark on this comprehensive guide to the kinds and advantages of welding solutions, we will dig into the ins and outs of numerous welding processes, reveal the benefits of MIG and TIG welding, and lost light on the specialized strategies that provide to special projects. One typical welding technique is Protected Steel Arc Welding (SMAW), additionally understood as stick welding.MIG welding, also recognized as Gas Steel Arc Welding (GMAW), offers distinct advantages over other welding processes, making it a recommended choice in manufacturing and automotive industries.Tungsten Inert Gas (TIG) welding, additionally recognized as Gas Tungsten Arc Welding (GTAW), stands out in the welding market for its exact control and high-quality welds.An additional prevalent arc welding approach is Gas Steel Arc Welding (GMAW), frequently referred to as MIG (Metal Inert Gas) welding.